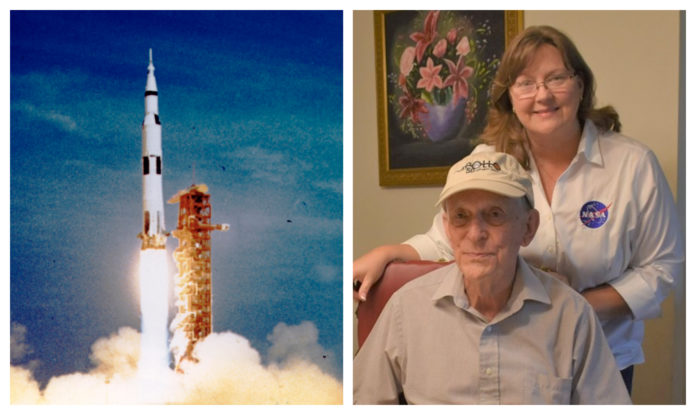
CULLMAN, Ala. – Today, the United States celebrates the 50th anniversary of the Apollo 11 moon landing, when Neil Armstrong and Buzz Aldrin became the first humans to set foot on the surface of the moon. Armstrong stepped onto the surface first, famously saying, “That’s one small step for man, one giant leap for mankind.” One Cullman man who watched the 1969 landing live on TV saw things that looked familiar to him, because he had helped build them.
This week, The Cullman Tribune sat down with Joe Hayden, who has been called the “Rembrandt of precision machining,” along with his daughter, NASA engineer Mary Hayden Hovater, in his west Cullman home. A master at machining, finishing and polishing metal, Hayden worked on components used in the Apollo 11 landing and other missions, including the Hubble and James Webb Space Telescopes, the space shuttle and a NASA experiment that required him to finish quartz spheres that hold the Guinness world record for the world’s most perfectly round man-made objects.
At 17, Hayden literally walked off from his parents’ farm and hitched a ride to town to enlist in the Army. After the recruiter drove him back home, since he was a minor, his mother signed a waiver and he was back on his way. He served on occupation duty in post-World War II Germany with one of the Ranger battalions of the 16th Infantry Regiment, 1st Infantry Division. After two years, he got out, but he was reactivated for the Korean War, during which he was assigned to the fabled 101st Airborne Division to work in training and operations (G3 for you military folks).
Between and after his military enlistments, Hayden worked as an administrative clerk for a construction company, as a night desk clerk in a hotel and after that, as a grocery clerk at Kroger.
Bored with the job and tired of the pay, according to Hayden, “I said, ‘The heck with this.’ I went to Michigan.”
Hayden may have been destined to create things from metal. In Michigan, the grandson of an Irish blacksmith (“I guess I just had a gene for it,” said Hayden.) took a job working in a machine shop, despite having no experience. He admitted to The Tribune he neglected to inform the foreman of that little problem, but he learned quickly by watching what other workers were doing. There, he became highly skilled at lapping, a process of finely shaping or smoothing surfaces.
After two years at that shop, which routinely laid off workers between projects, Hayden left to find something with more consistent job security, and found a small machining company called Speedring. The company would eventually locate a shop in Cullman and would change owners and names. Operating for years as Axsys Technologies, the plant is now part of the Precision Structures and Optics (PS&O) group of General Dynamics, situated right down Alabama Highway 157 from Hayden’s west Cullman home. He stayed with the company for 36 years.
Hayden said, “I can remember when we started; Speedring was pretty small then. I guess the whole building we was in wasn’t much larger than this house. But Speedring had always had a reputation of close machining, but when we got the contract to build these parts–you’ve got to realize that (tolerances, the amount of gap allowed between adjoining parts, in) an automobile engine is down in the thousandths of an inch. Well, this thing was in the millionths of inches, and so we bought new machines, tore them down and rebuilt them before they’d get closer tolerances.
“Then we had to hire the people to run them. And I remember one time, for one machine we hired five people before we got one that the foreman was satisfied with. But we probably had some of the best machinists in the world at Speedring at that time.
He continued, “They’d call for these parts to be checked at 68 degrees. Well, the building we was in was about 80 degrees all the time. So we didn’t have time to put in an air conditioner or nothing, so we took a wash tub and put a big piece of brass in the middle of it, and we put water in it and kept adding ice cubes to the water until we got our parts- and we set the gauge right in the center of them- until we got our parts down to 68 degrees. And they stayed there. They finally, before it was over with, they built a new building that was air-conditioned.
“Then we had a problem with- we couldn’t buy, commercially, instruments where we could check down that close, that would suit our needs. So, they hired a mechanical engineer that had just retired from the Navy, and hired an electrical engineer who’d retired from the Navy, and hired a mechanical engineer, and we designed and built our own machines to check down, to go down to one millionth of an inch. And some of those gauges are still being used today down at Axsys.
“But then we had to–the machines would only machine down to like one ten thousandths of an inch. We had to go down to like 10, 15 millionths of an inch. And whatever the tolerance was on these parts, we tried to make them half what the tolerance was: if it called for a hundred millionths of a tolerance, we tried to make it 50 millionths of a tolerance. When we got them off the machine, they wasn’t nearly down to the right correct size, so we had to work them down by hand.”
Hayden described precision work on articles of aluminum and beryllium, a rare metal lighter than aluminum but stiffer than steel. Speedring manufactured guidance system components and fuel cells for the Apollo command module, as well as guidance system components for the lunar module, the craft that actually touched down on the moon.
Said Hovater, “If it wasn’t for them, they wouldn’t have been able to land or get off the moon.”
In a document provided by General Dynamics, Program Manager Troy Wesson wrote:
“The mirrors in the Apollo guidance system ‘required surface flatness to 1/10 wavelength (which) must be completely stable under all conditions of space flight. Such requirements would be practically impossible without the use of beryllium as the mirror substrate.’ (1970s Speedring brochure) They were installed in a precision instrumented sextant manufactured by Kollsman Instrument Corporation utilizing a design by MIT and were ‘used to determine the Command Module’s position and attitude with relation to stars or landmarks. This data was then supplied to the onboard computer to calibrate the spacecraft’s Inertial Measurement Unit.’ This was a ‘a critical component of the spacecraft’s navigation system’ (from a description on icollector.com in an item auction). Apollo 8 Astronaut William Anders called Speedring’s optical unit assembly ‘an important part of the primary guidance navigation system of the Apollo command module.’ (Detroit Free Press, June 20, 1969).”
Hayden and his coworkers were initially kept in the dark about the final destination of the equipment they were building, and they were required to hide what they were doing from others.
Said Hayden, “It was more or less a secret thing. When we had visitors come into the shop, they’d cover the machines up with a tarp where nobody could see them. Kept it kind of quiet, what they was doing, because of the competition, you know. But we never saw the parts after they were finally machined. We made parts and somebody else put them together. I guess they went together okay, because they said they worked flawlessly.”
By the time of the July 1969 moon landing, the Speedring staff had been informed about the nature of its project, so Hayden got to watch the event live on TV with full knowledge that what he was seeing included his own handiwork.
Smiled Hayden, “We was proud of what we done, you know. It was amazing; we couldn’t believe it. Then, after we landed, I was thinking, ‘They’re never going to get off of there.’ I’ll bet they were thinking the same thing!”
Hayden was also called on to polish a mirror module that would travel to the moon with Apollo 11. He showed The Tribune a copy of a photo of Buzz Aldrin carrying it from the lunar module to install it permanently on the moon’s surface, where it and modules installed on later missions are still being used today to make calculations about the rotation and relative positions of the earth and moon, among other things. Fans of the TV show “The Big Bang Theory” may remember an episode in which the characters shot a laser at one of these modules from the roof of their apartment building (Yes, the moon mirror is really a thing!).
Hovater said, “It’s kind of neat; I can look up and say there’s a little piece of my daddy up there! I think that’s really cool.”
After the Apollo program concluded, Speedring, which had relocated from Michigan to Cullman- allowing Hayden to return home- continued its work with NASA and the U.S. military. Hayden worked on the assembly that held the Hubble Space Telescope during launch and released it into orbit, built beryllium window frames for space shuttles, worked on the James Webb Space Telescope and built gyroscopic components for missile and aircraft guidance systems. He even went the other direction from outer space and manufactured bearings for submarines.
Among his prouder achievements was the lapping of four quartz spheres that were used as gyroscopes in the guidance system for NASA’s 40-year long (a record for a single continuous NASA experiment) Gravity Probe B project. The experiment proved two predictions made by Albert Einstein’s Theory of Relativity and garnered the spheres’ makers first and second place spots in the “Guinness Book of World Records” for the most nearly spherical object ever made by humans, records that still stand today. He started the project at the Speedring plant, and completed the project by hand, in the garage attached to his west Cullman home.
Most precision machining is done today by Computer Numerical Control (CNC) machines, but Hayden has his opinions about that: “CNC machines can’t get as close as we did by hand. Stuff they’re building nowadays is not as close; it might accidentally get a part that close,” he said with a smile, “but it’s too time consuming to do it like we used to do it, by hand, and get everything perfect.”
Watching 50 years of NASA history
The Tribune asked Hayden what he thought of watching the development of the space program.
He shared, “It’s amazing. I can remember when people’d hear an airplane and everbody’d run out to look at it, or hear a car come down the road and everybody’d run out and look. They never seen one except maybe once a week. And I can remember when very few people had radios, and the old wall telephones.
“To see as much happen between now and then, I’m wondering what 90 years from now’s going to be like. But some of that stuff is so interesting, that I would have done it without pay just to be able to do it, because I loved doing it and I loved to see what it was going in.
“I was lucky to have a job that I loved. A lot of people say that they hate to go into work every day. I worked 19 hours a day sometimes, trying to get some of this stuff out on time. I didn’t have to, but I did it because I was interested in it and I wanted to see it done.”
Hovater confirmed her dad’s claims, telling The Tribune, “He had a little side thing, and he kept it after he retired from Speedring: Hayden Precision Finishing, just doing little odd things on the side. He’d work 12 hours a day, come home, and then the family sometimes would get together, and we’d go work lap things and do stuff for businesses around town.”
Hayden agreed, “Yeah, I’d work 10 hours, and then come home and we’d work till midnight.”
Said Hovater, “Love like that of what you do, first of all, is lucky, if you can ever have a job that you love that much. But that’s the difference between okay at your job and absolutely fantastic at your job. I mean that’s- what a great example to watch, growing up.”
Hovater herself has worked with NASA for more than 26 years, where she is currently a technical manager. She gets to do everything from representing NASA at school programs to figuring out how to clean up the space debris that threatens satellites and spacecraft. She has checked rocket paints, performed radiation testing and spent many a happy day shooting stuff at materials to be used in space to test impact effects. She helped the shuttle program pick up the pieces after the Columbia tragedy, testing multiple components to make sure the next mission would be among the program’s safest.
Hovater has even worked on systems of NASA’s new heavy lifter, the Space Launch System (SLS), the most powerful rocket ever built by NASA, which will return humans to the moon. In future configurations, the SLS and its Orion crew vehicle may carry astronauts to Mars.
A more diverse workforce
One of the changes noted by Hovater is “more diversity, way more diversity, like we have our first center director at Marshall (Space Flight Center). You see a lot more women, even since I’ve been there.”
As a NASA engineer and project manager, Hovater has spent her career in a traditionally male-dominated field.
She said, “At Wallace (State Community College), I was doing pre-engineering, pre-mechanical engineering, that kind of stuff; draftsman. I was a draftsman for a while, as a matter of fact, when I first started working at Marshall- which I loved. But in the classes, all the way through my master’s (degree), there were two females in the class. There just wasn’t, and I don’t know why; I don’t know why. I just never could figure that out.
“But I had supportive parents, and the things around me supported me to do what I wanted to. It’s one reason when I talk to the kids, and I always have- and I’ve been to Wallace to do motivational speaking, too, about that: I don’t care if you’re a guy that wants to be a nurse. You know, non-traditional roles are awesome! Do it! If you love it, go do it.”
Building the future on the past
Over her 26 years, Hovater noted, “There’s more consistency than you would think, and even though, like, change as far as what the rocket’s going to be, there’s so much that’s consistent over those programs, even since Apollo.”
She noted that some things have to change and usually for the better, like tasks that once required computers that once filled large rooms at Marshall Space Flight Center, that can now be done on personal smart devices. Regardless of the advancing technology, though, NASA understands that remembering what came before is the key to making a smooth transition into the future.
“We build on what we learn, so thank goodness for that,” said Hovater. “It doesn’t get lost. You’re not rebuilding the wheel every time even though, sometimes to the public, it seems like it’s taking forever when it shouldn’t.”
For Hovater, NASA’s increasing cooperation with private industries like SpaceX and United Launch Alliance might mark the biggest change she’s seen, one she considers positive. She explained that, by allowing private industries to take over certain traditional NASA roles, the agency frees up its own resources to reach even farther, to places like Mars.
Hovater said companies like SpaceX are “not competitors, they’re partners, really. We’re working well with them. It doesn’t make us lose our identity, because we’re working SLS, which is a way bigger rocket that’s going to go way further. And I’m not talking about just moon, because that, in and of itself, we’re not just going there to make footprints and put flags up this time. We want to stay there. And the reason we want to go there is we want to go to Mars; that’s our ultimate goal.
“We’re going to go there; we’re going to build. I think we’re doing the Gateway, and that’s going to help us; it’s kind of like a space station outside of the moon. We go there, we’re going to study; we’re going to travel down to the moon and study. That’s our work platform for getting ready for going and living on Mars, that kind of thing. It’s a lot.
“There’s change, but there’s not, because everybody’s always been looking out there.”
From Cullman High School to Marshall Space Flight Center in five years
Cullman native Blake Parker developed a fascination with space in his pre-K days, and it never went away. A mere five years after his 2009 graduation from Cullman High School, he found himself at NASA’s Marshall Space Flight Center in Huntsville, working on the International Space Station (ISS) project.
In a note to The Tribune this week, he shared, “Looking back, things began around the 25th anniversary of the Apollo 11 landing, way back in 1994. The ensuing increase in enthusiasm over space exploration lit a fire in 4-year-old me that’s been burning ever since. I devoured everything I could on the subject, from learning about the glories of the Cold War Right Stuff era of spaceflight to excitedly following the Space Shuttle and Mars Pathfinder programs as they unfolded. I knew that I wanted to be a part of it somehow. I loved to build, to draw, to design and make things fly, and it seemed like a natural fit.
“Paralleling my love of the technical, I was also developing a love of the scientific. I remember being absolutely blown away by the pictures taken of the outer planets by the Voyager missions, and of deeper space by the (then) recently-launched Hubble Space Telescope. Meanwhile, I surveyed the night sky with my own modest telescope and marveled at the mysterious Hale-Bopp comet as it swung by Earth in 1997.
“It wasn’t until the airing of a documentary on the History Channel in 2003, called ‘Failure is Not an Option’ based on the book by Gene Kranz, that I knew for sure I wanted to be an engineer. Kranz was one of the founding fathers of NASA’s Mission Control, and the program detailed evolution of the team of engineers that flew every mission alongside the astronauts of the Mercury, Gemini and Apollo programs without ever leaving the ground. Their quick thinking and expertise turned potential disaster into some of NASA’s finest moments. Knowing my chances of becoming an astronaut were incredibly slim, this was my ticket to space. I knew it was by no means an easy or safe path, but one that was worthwhile.
“Throughout my later schooling, the desire to be part of humanity’s efforts to venture beyond our tiny corner of the cosmos is where I drew my focus. I was definitely an oddball in the top of my graduating class of 2009 at Cullman High School as one of the few not going into the medical field.
“I graduated from the University of Alabama in Huntsville in 2013 with a bachelor’s in Aerospace Engineering. Following a brief stint as a student researcher with the U.S. Army, I finally got my chance to work with NASA thanks to Teledyne Brown Engineering in late 2014, 20 years after the dream first began.
“Currently, I work as stowage flight controller with the Payload Operations and Integration Center (POIC) at the Marshall Spaceflight Center in Huntsville. The POIC operates 24/7/365 in concert with control centers in Houston, Texas; Munich, Germany; Tsukuba, Japan; and other researchers the world over. It is responsible for overseeing the various science experiments that are done in and on the U.S.-owned parts of the International Space Station and providing real-time assistance to the astronauts on board. These experiments include everything from improving weather forecasting to materials science, to pharmaceutical research, all the way to particle physics. The work we do will benefit people on Earth, lay the groundwork for journeys back to the moon and beyond and improve our understanding of the universe around us.
“It’s been amazing to work with such a talented and diverse group of individuals. My team alone, which is responsible for keeping tabs on the location of NASA-owned science hardware on the station, has people with backgrounds in chemical engineering, civil engineering, aerospace engineering, biology and math, to name a few. Experience ranges from people who worked shuttle and Spacelab while I was still in primary school all up to recent college grads. Everyone has something unique to bring to the table.
“Every day I get to go into work and see an exciting new generation of spaceflight unfolding in the places that once held the giant machines and people of Apollo. It’s an incredible feeling for sure.”
Current NASA projects and the north Alabama connection
For Alabama, NASA’s not all rocket science; it’s also money and jobs.
A statement from NASA said, “Marshall directly employs nearly 2,500 civil service workers across the nation. Moreover, for every civil servant employed, approximately 14.2 additional jobs are supported throughout the economy. These jobs come in the form of contractors and also the dentists, retail workers, school teachers and others necessary to support the employment base. Additionally, those employees spend money in their communit(ies), thereby generating significant tax revenues for area economies. Throughout the United States, Marshall supports nearly 38,000 jobs and generates a total economic output of nearly $7 billion along with $830 million in federal, state and local tax revenues.”
Large rocket components have to come from large manufacturing operations, but large components are made up of lots of small components. More than half of Marshall’s contracts are sourced to Alabama suppliers, sometimes even small family-owned fabrication shops in places like Russellville and Guntersville. Most everyone around the Cullman area has a friend or neighbor who commutes to work at Redstone Arsenal or one of the many tech companies around Huntsville that support aerospace industries. Marshall has many ongoing projects that support the jobs of more than 17,000 north Alabama residents and contributes more than $70 million to the region through state and local taxes.
NASA’s media office says about the current SLS program:
“The economic impacts of SLS are heavily concentrated in Alabama. The SLS program supports 13,000 jobs and approximately $55 million in state and local taxes annually. Additionally, a large segment of SLS contracts, nearly $950 million worth, are sourced in Alabama. The total economic impact of SLS in the state of Alabama is $2.1 billion.”
Local impact: Cullman County students manufacture space station components
NASA’s reach into Cullman County isn’t limited to only Speedring/General Dynamics. At the Cullman Area Technology Academy (CATA), precision machining students are manufacturing aluminum components for the ISS. The school is participating in NASA’s HUNCH program (High Schools United with NASA to Create Hardware), which works with tech schools like CATA across the country to produce components for the space program. CATA is one of approximately 150 schools in 29 states currently participating in the project.
CATA students have manufactured sets of three panels that cover access ports on the doors of stowage lockers that can be used to transport anything from scientific experiments to containers of ice cream up to the ISS. Multiple access ports allow part of the cargo in the container to be accessed without having to expose all the contents. CATA students machined and drilled holes in the aluminum panels to tolerances of within five one-thousandths of an inch, a margin of error about the thickness of a sheet of common printing paper.
According to HUNCH Project Manager and ISS Simulation Engineer Bob Zeek, the students will get to sign their names on components headed to the ISS.
CATA Principal Billy Troutman told The Tribune, “They’re allowing students the opportunity to build precision machining skills, but they’re building hardware parts for NASA. These are locker doors that’ll be in the International Space Station. So that part of it, that’s just cool, no matter what.
“Precision machining parts are cool, no matter what, anyway, because you’re building something that’s going to be used. The fact that they’re building stuff for NASA’s just really neat. And the beauty of it is, they provide- obviously- the material, and they also provide tooling- be it hardware, blades, bits, equipment like that, as well, so it’s a win-win for us.”
During a visit to the school earlier this year, Zeek talked to The Tribune about the quality of the components produced at CATA:
“I was telling the kids earlier: Boeing used to make these parts, and Boeing still does these parts, but if you put them side by side, you couldn’t tell a bit of difference. The fact that the students learn the concepts of material traceability, quality assurance, spec’ing out the parts, not just running them on the machine, but the visual part of it, too, it’s phenomenal. We get very few rejects, because the kids are eager and want to learn, and they want to put their brand on it and say, ‘I did that.’”
Speedring’s space program legacy continues
Speedring, as the Precision Structures and Optics (PS&O) group of General Dynamics, continues to contribute to the U.S. space program.
General Dynamics Project Manager Troy Wesson wrote: “Today, through various acquisitions (acquired by General Dynamics in 2009), we are still proud to be the largest machining operation of exotic metals in the United States and are still the largest producer of beryllium structures and optics critical to our aerospace and defense programs. Under Maritime & Strategic Systems, PS&O is headquartered in Cullman, Alabama with over 120,000 sq. ft. of manufacturing space. The Rochester Hills, Michigan facility houses an additional 29,000 sq. ft. Together, the 250+ employees design, manufacture and integrate precision structures, reflective optics/telescopes and fast steering mirrors in support of the latest national and international commercial, defense and space-based applications. When failure is not an option, customers come to PS&O for their capabilities, focus on quality and ability to deliver mission-critical products. To learn more about PS&O: https://gdmissionsystems.com/en/services/beryllium-machining
“Although we are celebrating GD-MS’ heritage on Apollo 11, their NASA legacy pre-dates Apollo and has continued for generations. PS&O’s products and heritage are in orbit and flying through the stars on various satellites, telescopes and spacecraft to include: Gemini, Voyager, Gravity Probe B, GLAS, CATS, ATLAS, JPSS (ATMS, VIIRS, CrIS, RBI), GoSat, Gladiator, ICESat, Iridium, Mars Rovers, GOES (ABI), Himawari (ABI), CoStar, MPOES, Hubble and the Space Shuttle (to name just a few).
“Today, for NASA, PS&O is building instruments and optics for Joint Polar Satellite System with the VIIRS and CrIS mirrors and telescopes. They also have a proud heritage of being the organization that machined the 18 primary mirrors (plus spares, secondary and tertiary mirrors) for the James Webb Space Telescope scheduled to launch in March 2021. Rest assured that when James Webb launches, the team members will be listening to regularly broadcasted reports, just like they did back in 1969.”
Marshall Space Flight Center recently released this statement on Alabama’s relationship to NASA and its programs:
From Alabama to the Moon
The path to the Moon has run through Alabama since the earliest days of our nation’s space program. Today, work in the “Rocket City” Huntsville and across the state is advancing the largest rocket we’ve ever built and our Artemis Program to land humans on the Moon by 2024. At a recent visit with the Huntsville Chamber of Commerce, NASA Administrator Jim Bridenstine demonstrated Alabama’s deep technical and economic contributions to our nation’s space program. A $1.6 billion amendment above the President’s request of $21 billion for NASA’s Fiscal Year 2020 budget will accelerate our progress to the Moon and solidifies that the state’s importance to our exploration efforts.
NASA’s Marshall Space Flight Center in Huntsville creates significant economic impact by supporting thousands of jobs and investing millions of dollars in research and development. It helps drive an innovation-based economy in Alabama and throughout the United States. The center generates contracts across nearly every category of manufacturing or service production. And NASA reaches all 67 Alabama counties through education, business, partnerships, and other innovative ways to engage the state with our ambitious national goals.
Much of the Marshall’s work is tied to the Space Launch System (SLS) rocket that will power human exploration of the Moon and a new generation of missions. SLS is America’s rocket, with men and women from almost every state working hard every day to move America forward to the Moon. And it’s also a critical part of Alabama’s legacy of mission-critical design, development and integration of the systems for space exploration and scientific missions.
Our plans to land humans on the lunar South Pole by 2024 build on Marshall’s expertise. The rocket scientists at Marshall designed, built, tested, and helped launch the giant Saturn V rocket that carried Apollo astronauts to the Moon. They also developed new rocket engines and tanks for the space shuttles, built sections of the International Space Station, and now manage all the astronauts’ science work aboard the station from a 24/7 Payload Operations and Integration Center.
SLS and the Orion spacecraft in which astronauts will travel to the Moon are the backbone of our sustainable deep space exploration systems. Among recent progress, the SLS team has recently:
- Built and tested the SLS solid rocket boosters and the core stage rocket engines.
- Moved the 66-foot-tall forward part of the rocket’s massive core stage. This helps prepare for its final assembly and integration to the liquid hydrogen tank.
- Delivered the Pathfinder, a full-scale simulator of the rocket’s core stage. This is the same size, shape and weight of the massive real thing, and will help us learn to work with it.
- Loaded a test version of the enormous liquid hydrogen tank that fuels the rocket’s RS-25 engines into a test stand at Marshall. There it will be exposed to simulated stresses of a space launch.
- Outfitted the SLS launch vehicle stage adapter, which connects the core stage of the rocket with its interim cryogenic propulsion stage.
Astronauts will travel to the Gateway in lunar orbit for expeditions to the surface of the Moon. Marshall is supporting development of potential deep space habitation element for Phase 2 of the Gateway, which will help the agency establish sustainable missions on and around the Moon by 2028.
Marshall and Alabama have also played key roles in additive manufacturing or 3-D printing — from rocket engine development advances to 3-D printing on the station. This technology has revolutionized what we are able to do in space, where mass and space are big considerations.
Demonstrating Alabama’s importance to our space program, NASA has invested millions in local university programs and in contracts with businesses large and small. Marshall has more than 50 active Space Act Agreements with industry, academic, non-profit and other government agencies based in Alabama, including the University of Alabama System, Auburn University, Alabama A&M University in Huntsville, and the University of North Alabama in Florence.
Next generation STEM leaders from across the world also gain important experience through Marshall’s Student Launch and Rover Challenges.
Our presence in Alabama is leading to a human presence on the Moon. Throttle up!
Copyright 2019 Humble Roots, LLC. All Rights Reserved.
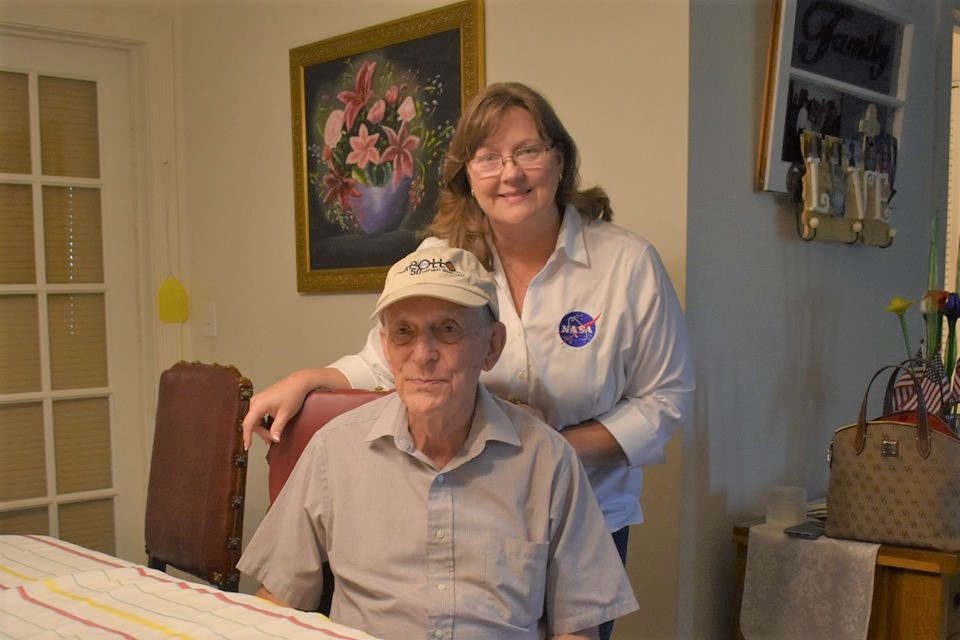
Pushing the limits of space exploration for two generations: former NASA contractor Joe Hayden with daughter and current NASA engineer Mary Hayden Hovater (W.C. Mann for The Cullman Tribune)
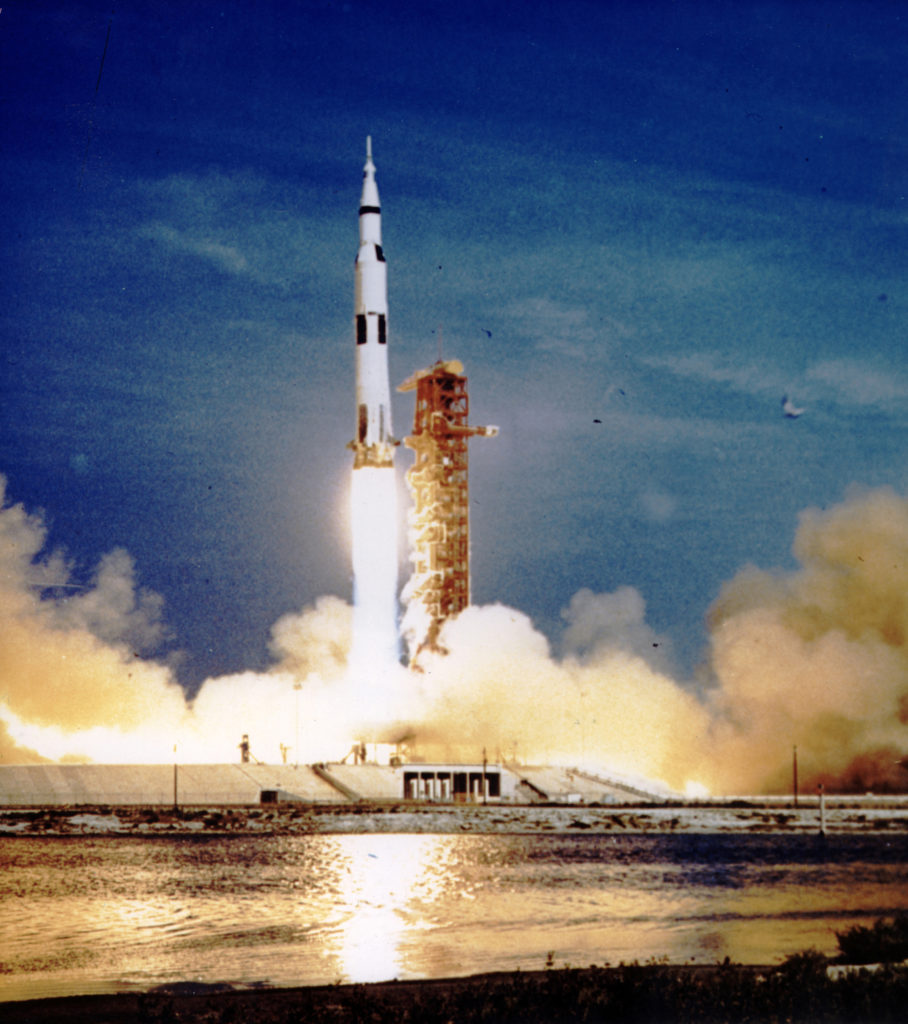